Aluminum die casting parts have a wide range of uses across various industries, owing to their numerous advantages such as durability, lightweight, and cost-effectiveness. Here are some common uses of aluminum die casting parts:
1. Automotive Industry: Aluminum die casting is extensively employed in the automotive sector for parts such as engine blocks, transmission cases, cylinder heads, and wheel spacers. The use of aluminum die casting in automobiles helps to reduce weight, increase fuel efficiency, and enhance overall performance.
2. Electronics and Electrical Industry: Aluminum die casting parts are utilized for various electronic and electrical components such as heat sinks, connectors, housings, and brackets. These parts provide efficient heat dissipation, excellent electrical conductivity, and offer protection to delicate components.
3. Aerospace Industry: Aluminum die casting is widely adopted in the aerospace industry for manufacturing aircraft components, including engine parts, structural components, and interior fittings. Aluminum die casting offers excellent strength-to-weight ratio, which is crucial for achieving fuel efficiency and enhancing aircraft performance.
4. Industrial Machinery: Aluminum die casting parts find applications in the production of industrial machinery such as pumps, valves, compressors, and machine tool components. These parts offer high precision, dimensional stability, and durability, contributing to the efficient functioning of machinery.
5. Consumer Goods: Aluminum die casting parts are commonly used in the production of consumer goods like kitchen appliances, sporting equipment, and furniture components. They provide an attractive finish, corrosion resistance, and high strength, making them ideal for diverse consumer applications.
6. Telecommunications: Aluminum die casting parts play a significant role in the telecommunications industry, particularly in the production of cellular phone components, satellite communication devices, and antenna systems. These parts offer structural stability, electromagnetic shielding, and easy integration of various components.
7. Medical Equipment: Aluminum die casting is employed in the manufacturing of medical equipment such as diagnostic devices, prosthetics, and surgical instruments. The use of aluminum die casting ensures high precision, cleanliness, and resistance to sterilization processes required in the medical field.
In summary, aluminum die casting parts are utilized across various industries, ranging from automotive to aerospace, electronics, industrial machinery, consumer goods, telecommunications, and medical equipment. Their exceptional qualities make them a preferred choice for manufacturers wanting to achieve strong, lightweight, and cost-effective components.
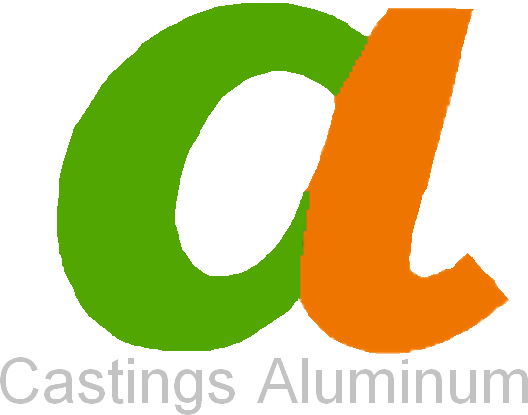
If you are looking for information about
Aluminum Casting Tooling and Molds, look at this website.
If you are looking for information about
Aluminum Casting Handtool Parts, or also
Aluminum Box Parts, take a look at this website.
Castings Aluminum Company Die Casting Company
6918 Beck Avenue
North Hollywood, CA. 91605
818-982-9200 Phone
For Aluminum Part Prices, send email request to Sales@Castings-Aluminum.com.